Among the many tools available to cosplayers, 3D printing has become one of the most valuable. It provides an efficient and precise way to create intricate, wearable accessories that might otherwise take weeks or months to craft. From helmets and armor to jewelry and detailed props, 3D printing allows cosplayers to replicate designs with unmatched accuracy.
Why 3D Printing Is Perfect for Cosplay
Cosplay often demands high levels of detail and customization. Accessories need to be accurate to the source material, durable enough to withstand wear, and comfortable for extended use. Traditional crafting methods, while effective, can be labor-intensive and limited in their ability to capture intricate designs.
This is similar to how creative digital experiences, like the dynamic gameplay of the spribe aviator, thrive on precision and attention to detail. Just as successful cosplay relies on meticulous design and planning, games like Aviator engage players by blending strategy with a focus on timing and calculated moves.
Advantages of 3D Printing
● Precision and detail: Advanced 3D printers can create fine details, making it possible to replicate even the most complex patterns or engravings.
● Customization: Digital models can be tailored to fit specific body sizes and shapes, ensuring a perfect match for the cosplayer.
● Efficiency: 3D printing allows you to rapidly prototype, modify, and finalize designs, saving significant time compared to traditional crafting methods.
● Material variety: Different filaments can be used to achieve specific properties, such as flexibility, strength, or lightness, depending on the accessory.
Let’s say you’re designing an armored gauntlet. With 3D printing, you can create a detailed, lightweight piece that perfectly matches the original design and fits comfortably on your arm. This level of customization is difficult to achieve with materials like foam or metal.
The Basics: Tools and Materials
To get started with 3D printing for cosplay, you’ll need three main components: modeling software, a 3D printer, and filament. Here’s what to look for in each.
3D Modeling Software
The journey begins with a digital model of your accessory. If you’re new to 3D design, software like SelfCAD is an excellent choice due to its user-friendly interface and robust features. Here’s what makes a good modeling tool:
● Ease of use: Look for intuitive tools that let you sketch, sculpt, and edit your design without a steep learning curve.
● Templates and tutorials: Pre-made templates can save time, and tutorials can help you refine your skills.
● Slicing integration: Some programs allow you to prepare your model for printing directly, eliminating the need for separate slicing software.
SelfCAD, for instance, offers all these features, making it a popular choice for cosplayers who want a seamless transition from design to print.
3D Printers
The choice of printer depends on the size and complexity of your project. Here are some features to consider:
● Build volume: Larger accessories like helmets require more space.
● Print resolution: Higher resolution ensures finer details and smoother surfaces.
● Heated bed: Essential for materials like ABS to prevent warping.
Filament Types
The filament you choose affects the look, feel, and durability of your accessory. Here are the most common options:
● PLA (Polylactic Acid): Easy to use, biodegradable, and suitable for detailed props. However, it’s less heat-resistant.
● ABS (Acrylonitrile Butadiene Styrene): Durable and heat-resistant but prone to warping. It requires a heated bed.
● PETG (Polyethylene Terephthalate Glycol): A great middle ground—strong, heat-resistant, and easy to print.
● TPU (Thermoplastic Polyurethane): Ideal for flexible parts like straps or hinges.
For example, a helmet might use PLA for its outer structure due to its detail capabilities, while the internal padding could be made from TPU for comfort.
Designing Your Accessory
Gather reference images from multiple angles to ensure accuracy. Pay attention to proportions, details, and textures. For wearable items, take your body measurements or the measurements of the person who will be wearing the accessory.
Use Digital Modeling Techniques
Build the base shape using basic geometric forms. Then, use sculpting tools to carve grooves, add embellishments, or mimic textures like leather or metal. Scale your model to match your measurements. Many software tools allow you to visualize how the piece will fit.
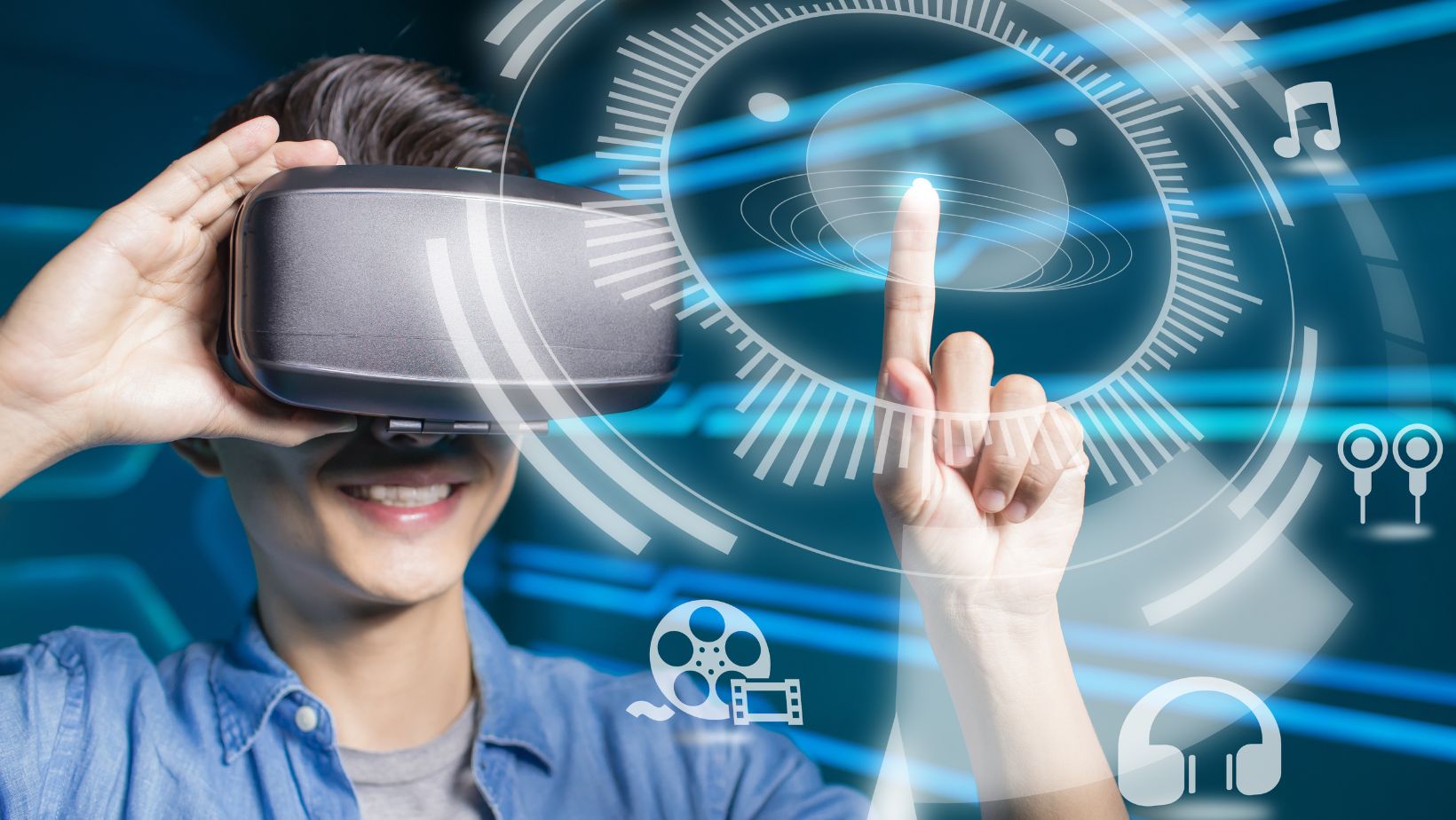
Let’s say you’re designing shoulder armor. Begin by sketching a simple curve to match the shoulder’s shape, then add layers of detail, such as ridges or engraved symbols.
Preparing the Model for Printing
Once your 3D model is complete, the next step is to prepare it for printing using slicing software. This critical step ensures that your digital design is transformed into precise instructions that your printer can understand.
Key Slicing Settings
Layer Height
Layer height determines the thickness of each printed layer. It directly affects the quality and print time of your model:
● Lower layer heights: Settings like 0.1mm produce smoother surfaces and capture intricate details better. This is ideal for cosplay accessories with visible details, such as engraved patterns or fine textures.
● Higher layer heights: Settings like 0.2mm or more reduce print time but can leave visible lines. These settings work for internal or hidden parts of accessories.
For example, if you’re printing a helmet, you could use a lower layer height for the outer shell and a higher one for internal structural pieces.
Infill Density
Infill density controls how much material is used inside the print. 10–20% infill is common for wearable items like armor pieces. It provides sufficient strength while keeping the item lightweight. Use 50% or more if the piece will experience stress, such as prop weapons or load-bearing connectors. Infill patterns like hexagonal or grid structures can maximize strength while using less material.
Supports
Supports are temporary structures printed to hold up overhanging parts during the process:
● Where to place supports: Identify overhangs greater than 45 degrees. These areas are prone to sagging or failing without supports.
● Strategic placement: Position supports where they are easy to remove, such as on the inside or less visible parts of the model. For example, supports inside a helmet can be removed without affecting its external appearance.
● Minimize post-processing: Excessive supports can increase cleanup time and risk damaging the piece. Consider angling the model slightly during slicing to reduce the need for supports.
Printing the Model
Once your slicing settings are optimized, it’s time to move to the printing phase. This stage is where preparation and attention to detail make the difference between a successful print and a failed one.
Printer Setup
- Level the bed: Use the leveling feature on your printer or a manual adjustment process. Uneven beds can cause poor adhesion, leading to warped or failed prints.
- Clean the nozzle: Residual material in the nozzle can block proper filament flow, affecting print quality.
- Preheat: Set the correct temperatures for the filament (PLA: 190–220°C for the nozzle and 60°C for the bed; ABS: 220–250°C for the nozzle and 100°C for the bed; PETG: 220–250°C for the nozzle and 75°C for the bed).
Printing Process
For larger pieces, consider splitting the model into smaller sections. This makes printing easier and reduces the risk of failure. Assemble the sections using connectors, adhesives, or dowels.
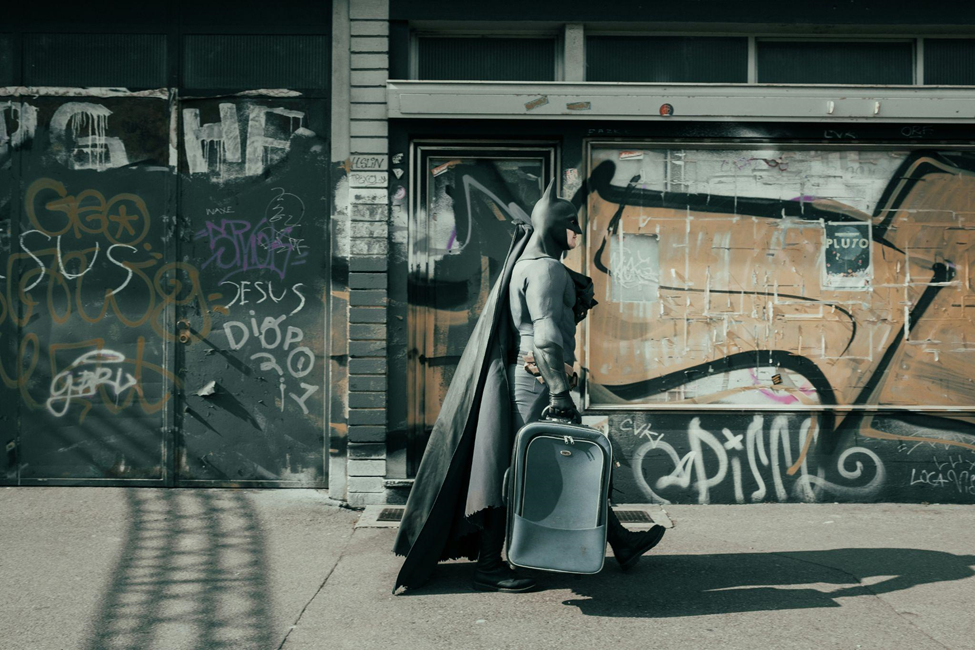
Monitor the print, especially during the first layers, to ensure proper adhesion. Depending on the size and complexity, a print can take anywhere from a few hours to several days.
Post-Processing: Turning Prints into Wearable Art
Step 1: Removing Supports
Support removal can leave rough edges or even tear sections of the model. Use slow, deliberate motions. For stubborn supports, lightly heat them with a hairdryer or heat gun to make removal easier.
Step 2: Sanding
Sanding smooths the surface and removes visible layer lines. Start with coarse sandpaper (around 120 grit) and progress to finer grits (400–800) for a polished finish. For a truly smooth finish, especially on curved surfaces like helmets, wet sanding with fine-grit paper can yield professional results.
Step 3: Priming
Apply a primer to create a uniform surface. Apply two to three thin layers, sanding lightly between coats for an ultra-smooth surface. Use a gray or white primer for light-colored paints and a black primer for darker finishes or metallic effects.
Step 4: Painting
Use acrylic paints for vibrant colors. Start with a solid base color that matches the core material of the design (e.g., silver for metal armor). Add layers gradually and let each dry before applying the next. Techniques like dry brushing or airbrushing can create effects such as weathering or metallic finishes. Use fine brushes for intricate patterns or highlights.
Testing and Iteration
3D printing shines when it comes to iteration. Before committing to a full-scale print, test the design by printing smaller sections or simplified versions. This approach saves material and allows you to fine-tune dimensions and details. For example, you could print just the base of a helmet to verify the fit before adding intricate designs.
To Sum Up
As you dive deeper into 3D-printed cosplay, you’ll discover that it’s not just about replicating a character’s look but about making something entirely your own. Mistakes will happen, and that’s part of the journey. A warped piece or an uneven paint job often leads to creative solutions that enhance your skills and improve your designs. Every misstep teaches you to think like a maker, not just a fan.
With the growing accessibility of 3D printing, cosplayers now have the tools to push boundaries and even inspire others to embrace this hybrid of craft and technology. Your next printed accessory could perfect your cosplay and open doors for new collaborations.